F-ending O-ff D-isaster
FOD means different things to different people. To some it spells
'foreign object damage', to others it's the cause of the problem and
stands for 'foreign object debris'. But, whatever you deduce from
the acronym, it's nearly always financially expensive and can –
in the worst circumstances – cost lives. Geoff Thomas reports.
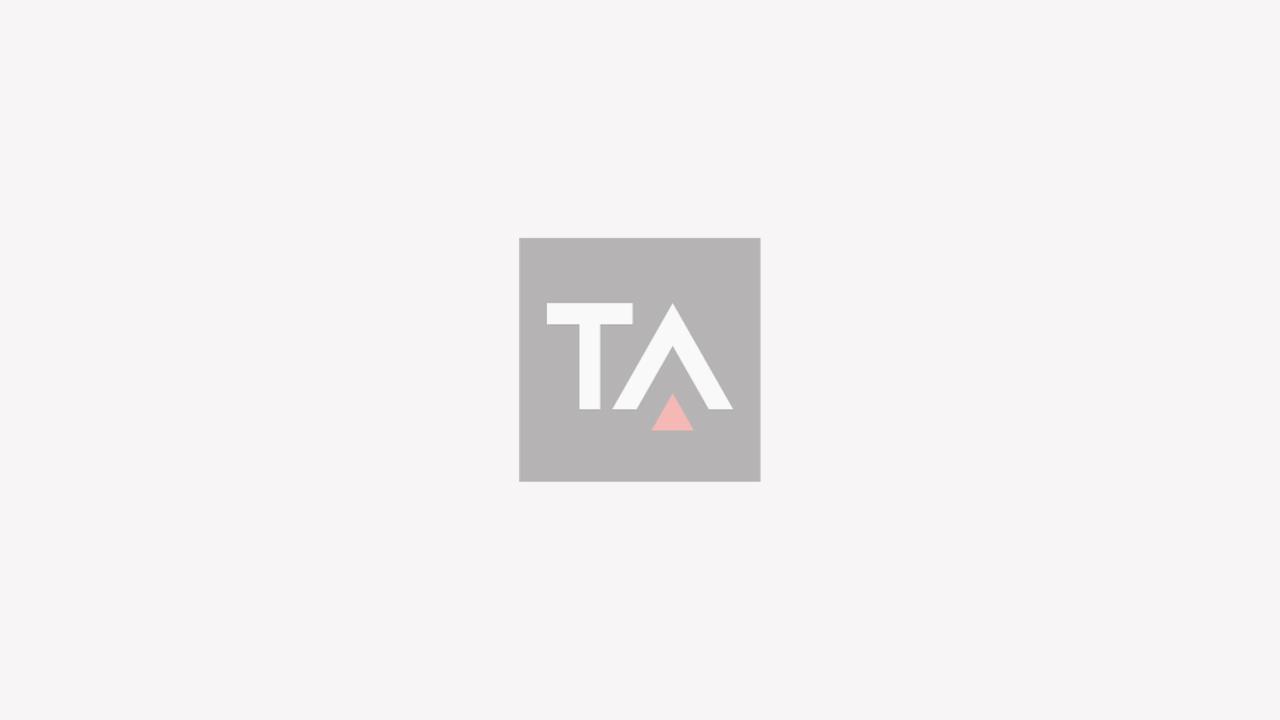
Think of the infamous Concorde crash at Paris in 2000 that was caused, said the official report, by a tyre being punctured by rolling over a piece of metallic runway debris…but more of this later.
FOD is estimated to cost the global aerospace industry $12-billion a year. Around $4-billion is the direct cost for damaged parts. However, another $8-billion is taken up with indirect costs such as delays, plane changes, fuel costs, significant damage to aircraft and parts and even death and injury to workers, pilots and passengers.
Nobody has quantified the cost to the industry in the Middle East – but it is certain to be a considerable sum, especially considering the disadvantageous climatic and infrastructural issues prevalent in the region.
Airliners – and particularly their engines – are highly vulnerable to damage from the sort of debris that can often be found on airport aprons and runways. Tools, plastic bags, luggage, cargo straps, containers, loose parts, rocks, chunks of concrete, sand, clothing…the list is endless.
And, once a piece of FOD has been sucked into a running engine, the damage is likely to have been done. At best it may be expelled at high speed, causing damage to nearby aircraft and/or people, while at worst it can cause serious (even terminal) damage to fans, compressors, combustors and turbines.
Anyone who has attended an airshow, particularly when the airfield in question isn’t used regularly for intensive military or commercial flying, will have witnessed a pre-show ‘FOD walk’ before the display aircraft arrive. Frequently the walkers comprise a line of military cadets, briefed to walk slowly along the active runways while examining the surface and surrounding terrain and taxiways for debris and/or damage. They’ll often be joined by a series of vehicles, where the driver and passengers are also responsible for identifying and collecting FOD. This is time-consuming and also expensive but it’s vital work that helps to prevent damage and helps to prevent accidents too.
At busy commercial airports around the world, vehicles patrol the environs of the airfield at frequent intervals, sometimes delaying flight arrivals and departures. However, two airports in the Middle East – Doha and Dubai – have joined London’s Heathrow and the airports at Vancouver in Canada and the USA’s Providence, Rhode Island, by pioneering attempts to prevent FOD becoming more than a costly nuisance by installing a new system produced by British company Qinetiq.
Called Tarsier, the system uses radar and ultra-sensitive cameras to detect even small objects that may be lying around at airports and which may be ingested by engines.
In two years’ operation at Vancouver International Airport, Tarsier found more than 250 items of FOD, including several classed as ‘posing significant risk’. On one occasion Tarsier detected an earthing cable. Left undetected this could have caused a major incident.
In some cases Tarsier has also enabled users to halve their FOD retrieval time, providing runway capacity gains of up to four slots during peak hours. And today, in particular, slots are a valuable, tradable commodity.
Quinetiq’s Tarsier is a millimetric-wave radar system that can detect objects on the runway surface so they can be precisely located and collected, even at night and in poor visibility. With London Heathrow’s ultra-busy runways operating at 98 per cent capacity, there’s little time to spare to drive FOD vehicles along the tarmac and the airport operators believe that the system will improve timekeeping as well as safety.
The Tarsier system has completed extensive trials at Heathrow and is now in operation. Two radars scan the entire runway area 24h a day, locating objects – even small parts whether metal, plastic, glass, wood, fibreglass or organic matter – that could have fallen from aircraft or vehicles or even blown-in from the perimeter road.
A display unit in Heathrow’s operations centre provides the runway inspection team with a round-the-clock picture, allowing them to locate debris on the tarmac and retrieve it in a matter of minutes. This replaces the need to carry out vehicular visual runway patrols at least twice a day, during which the runway has to be taken out of operation, and improves on visual inspection, which can be unreliable in bad visibility.
Qinetiq’s Heathrow contract also includes the installation of high-specification day/night cameras that allows remote identification of debris. The ability to identify quickly a part that has detached from an aircraft can enable the crew to be advised of the details.
As well as FOD, Tarsier can detect the presence of birds and wildlife, aiding operators with wildlife management teams and helping to reduce the risk of bird strikes.
But it’s not only engines that are at risk. As mentioned at the start of this article, tyres are vulnerable to FOD damage – witness the fatal Concorde crash just after take-off from Paris Charles de Gaulle airport in 2000. That disaster was, according to the official accident report, caused by a sharp piece of metal debris that fell from a preceding aircraft and cut one of the supersonic airliner’s tyres. At high loadings and speed, the tyre exploded, causing a fierce fire after chunks of tread from the tyre struck the underside of the wing, where the resulting shockwaves ruptured the integral fuel tanks.
Until all airports have a FOD detection system, other techniques are being developed (one is an engine-mounted radar-based device being developed by the UK’s BAE Systems) to track small objects that may be sucked-in by aircraft engines while taxiing, taking-off and landing. A 12Ghz radar that could be installed as a permanent sensor on engines is in the final stages of development.
To detect blade damage, the device is designed to replace an engine’s endoscope inspection plug, while to monitor FOD another sensor is affixed in the inlet.
Developed by BAE Systems’ advanced technology centre in the UK, the radar can differentiate between stone and metal. This is important, because identifying the type of FOD helps engineers to determine what level of inspection needs to be carried out, potentially saving time and money.
The blade-damage sensor would be placed within the fan casing to fire radar waves at the rotating blades, identifying blade problems by detecting changes in their natural vibration. The data interpretation software is currently at the proof-of-concept stage and the system has been developed using an electrically driven – and Rolls-Royce-provided – Pegasus engine from a Harrier ‘jump jet’ at Bristol in the UK.
But it’s not only true ‘accidental’ man-made FOD that causes problems at the world’s airports. Some of them, especially those in dusty, sandy parts of the world, have considerable problems with polluted air being sucked-in by aircraft engines.
And the same sandy atmosphere can also cause excessive wear on wheel bearings, undercarriage components and brakes. It can even cause vital static ducts and apertures to become blocked and interfere with sensitive electronic equipment.
Airports surrounded by sandy terrain are frequently covered by a visible layer of granular material and this is inevitably sucked-in by powerful turbofans.
Engines like a clean and relatively cool atmosphere so starting-up, taxiing and taking-off in unpolluted air, means enhanced time-on-wing and this can amount to many thousands of hours extra running between shop visits.
Hot and dusty airports, in regions like the Middle East, North Africa and the Gulf, do not only experience relatively dirty air at ground level.
When airliners fly sectors between airports in the region, the air being compressed by the engines may also contain minute particles of dust and sand and this can cause excessive wear and even the build-up of glass-like material – not dissimilar to what happened when volcanic dust from Iceland caused travel chaos in Northern Europe early in 2010 – on hot components in combustors and turbines.
Over the years, many have tried to filter the air being sucked in by aviation turbofans – but so far with little success. The quantities and flows are just so huge that any encumbrances to smooth and free-moving air are just impossible, so the designers have to live with the fact that air pollution in some parts of the globe is going to cause more wear than in an ideal world.
Frequently, countries that experience a hot and relatively dusty atmosphere, tend also to have more wind-blown debris than is prevalent in cooler, cleaner climes. Engine original equipment manufacturers ( OEMs) have known for years, at least since the dawn of jet travel, that their equipment would have a considerably reduced life in hot, dusty parts of the world.
Just ask the people responsible for military jet turbine engine maintenance in Afghanistan. Even on helicopters, where filters and separators are sometimes used, the problem is still very real and the dust traps don’t go far towards solving the problem of highly abrasive material being ingested by sophisticated power-plants. The resulting reduction in time between overhaul (TBO) can be huge and by some estimates is as much as 50 per cent.
And, of course, it’s not only natural dust that causes difficulties. When the wind is blowing dust into the air, any man-made material left lying around – like plastic bags, buttons, pens, coins, cardboard cartons, magazines and wastepaper – can also be sucked into engines with frequently expensive results.
The cost of damage to an engine in a FOD incident can easily exceed 20 per cent of its new cost. And, with airliner turbofans costing upwards of $10-million each, this can be a massive sum to incur accidentally – especially when the damage is preventable.
Believe it or not, tools left in an engine after maintenance (or even from when the engine was built) is a real issue. It’s claimed that one engine OEM ‘loses’ thousands of dollars-worth of tools each month in just one of its plants.
Forgetting the value of the missing tools, the resulting damage from man-made FOD is even greater. So systems are now being put in place to produce toolboxes where a missing tool is identified with an optical sensor that automatically detects removal and replacement. And, to safeguard each individual tool, a user must identify him or herself by a PIN number or a swipe card! Rolls-Royce at Derby in the UK already has this system in place and it’s likely that other OEMs will follow suit.
So FOD is a major issue for airlines and aircraft operators around the world – but especially in places like the Middle East where climatic issues contribute towards the problem.
Part of the solution is good airport management and enhanced education for aerospace workers. However, where there is a hot, dry climate and it’s frequently windy, FOD will continue to be a challenging problem that inevitably results in more costly engine and airframe maintenance – a reality that has to be borne in mind in when vital business plans are being written.
Stay up to date
Subscribe to the free Times Aerospace newsletter and receive the latest content every week. We'll never share your email address.