Leaning towards more efficient management
Lean management, a global term increasingly talked about in almost every industrial sector, is now the focus of the Middle East aerospace industry. Alan Martyn of Simpler Consulting clears up the confusion surrounding the subject, explains how it is suited to the region and looks at best practice.
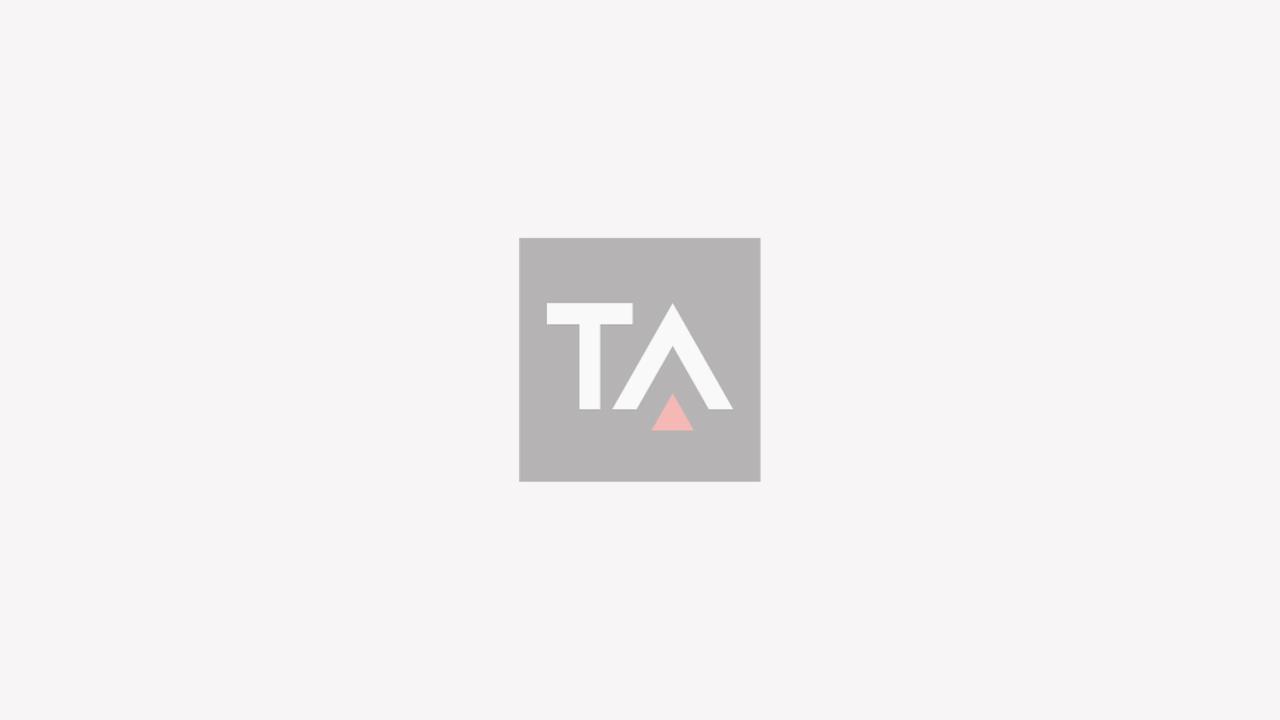
Lean is considered by some to be the most effective method of ensuring a company is running as efficiently and cost-effectively as possible. However, many people in the commercial and military aerospace and MRO sectors still lack understanding about what it involves and how it should be implemented.
Adding to the challenge for Middle Eastern organisations is an underlying scepticism about whether the lean management approach can survive the cultural differences inherent in the region.
Perhaps the best way to understand the potential benefits is to look back at the history of the methodology and where it originated.
The lean management approach can be traced back to an integrated socio-technical system developed by
Although recent events have somewhat soured
The extent to which the principles have spread across the globe indicates the relative ease with which they can be transferred across regional and cultural borders, lending support to the argument that the benefits can be brought to the Middle Eastern aerospace industry.
While the lean approach has long been used by Western aerospace and defence manufacturers in the production environment, its integration into
Whether in a commercial or military fleet, the demand to deliver the right level of capability is a daily challenge. The US Air Force faced two choices: invest in further equipment, or improve its maintenance processes to get more capacity from its existing fleet. It chose the latter and enlisted lean methods to support a re-evaluation of its maintenance operations.
By examining in detail the processes undertaken when an aircraft was docked for repair and maintenance, and redesigning them to ensure that each stage was as efficient as possible, the lean programme allowed the US Air Force to reduce the duration of the maintenance process by 35 per cent, with the number of days each aircraft was grounded reduced from 339 to 220. This allowed it to boost the capacity of its fleet, without needing to purchase a single additional aircraft.
After this first result, the use of the technique in the military expanded from MRO into frontline operations and command and control processes. This represented a significant development, showing that the process can be applied anywhere in a commercial or military operation.
The potential of lean management to help air forces enhance the efficiency and effectiveness of their existing fleets without the need for additional investment has sparked interest from a number of Middle Eastern air forces and commercial MRO providers. While some assume that “oil-rich states” are unconcerned about the efficiency of their operations, the reality is always quite different, and all are interested in getting more military capability from their fleets.
In this respect, lean techniques are ideally suited to the current situation of many Middle Eastern defence operations. Many have invested heavily in assembling a fleet consisting of the most advanced technology, but don’t necessarily yet have the processes in place to ensure that these fleets can be utilised to yield maximum operational capability.
A good first step in implementing a lean programme or improving existing initiatives is to pinpoint one particular area of business need where an initiative will have the greatest first impact. By identifying a financially or operationally significant part of the business that can be improved, lean programmes can quickly prove their worth and secure staff buy-in, without disrupting the company as a whole. It is very important that any improvement targets should be balanced in terms of delivery, quality, cost and personal aspects of an operation. For example a commercial MRO provider might aim to achieve the following four results in this initial project:
• 20 per cent financial savings;
• 30 per cent improvement in delivery turnaround;
• 25 per cent decrease in warranty defects;
• Improvements in human development – for example the cultural integration of a multinational workforce, reducing the transient nature of some staff and the accompanying knowledge loss.
Another crucial aspect of a successfully implemented lean programme is ensuring that each element is designed specifically for your organisation. Putting in place generic programmes is simply a waste of time – each company runs processes and methods of working that are unique.
Staff and cultural buy-in is a must too. Understandably, any meaningful change will only happen when the majority of staff sees something better.
One of the most common arguments made against the ‘imposition’ of outside management approaches is that they fail to take into account the nuances of local customs and culture when attempting to streamline operations. Indeed, the dangers of this are obvious. In the
The bottom-up approach of lean management ensures that potential tensions such as these are highlighted at an early stage and never become an issue since the change is “by the people for the people”. Local workers would not dream of changing something so culturally important to them, so it never becomes an issue, with lots of opportunities found elsewhere for lean-based improvement by the team.
Once success has been achieved in this first step it allows the concept to be rolled out to the rest of the business and facilitates the transfer of knowledge. This sharing of information is important and means that once the initial consultation period is over, staff at all levels have the knowledge to implement further enhancements. Improvement can continue throughout the entire business and knowledge gaps created by key personnel leaving the organisation can be prevented.
The fundamental benefits lean management can offer – improving productivity by making better use of existing resources – fit well with the goals of many organisations and air forces in the region, who wish to increase the effectiveness of their current equipment. Once initial concerns about the compatibility between lean methods and regional customs have been allayed, the sector stands to gain hugely from a more focused, streamlined approach to its operations.
Stay up to date
Subscribe to the free Times Aerospace newsletter and receive the latest content every week. We'll never share your email address.