Fake parts a real threat
Counterfeit parts are a threat to safety, reliability and profitability of operators and MROs alike. Chuck Grieve has been looking at the problem.
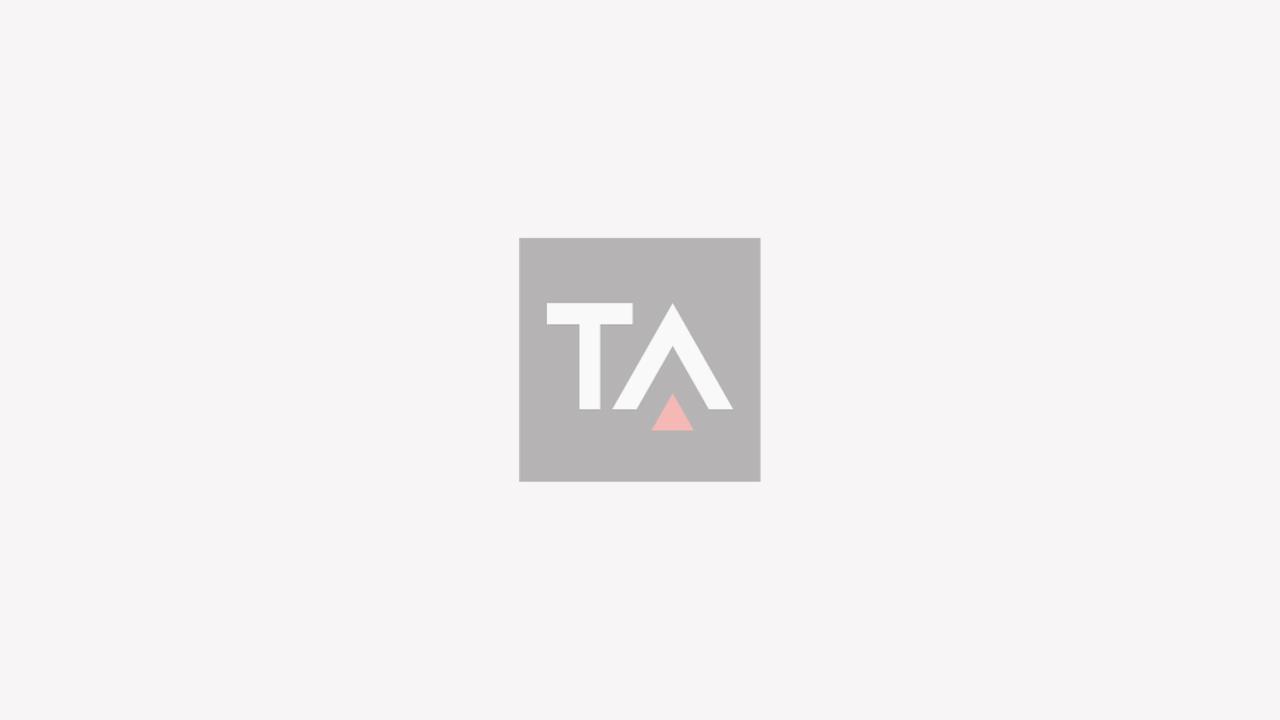
They’re called suspected unapproved parts – SUPs for short. When an industry gives something like that its own acronym, you know there’s a problem.
The Federal Aviation Administration (FAA) says 3,000 SUPs have been discovered since 2011, when they were simply called bogus parts.
Whatever the underlying causes – cost control pressures, profiteering, a shortage of genuine original equipment manufacturer (OEM) parts – where a demand exists, someone will act to fill it.
An industry source with links to the Middle East MRO sector said safety is the main issue with SUPs.
“Carbon brakes are typical,” he said. “Some countries manufacture their own because of the price of carbon. If an aircraft has unapproved parts installed, it’s not as certified, so it can’t have type approval. That invalidates its insurance. You can imagine the ramifications in the event of an incident.
“Some people out there want the cheapest part and their organisations use cost as the sole factor for procurement decisions. For us, if it’s too cheap, the alarm bells ring.”
The FAA is trying to introduce more stringent safety checks to ensure any parts entering the supply chain have the correct paperwork and the technical director does the final sign-off. “Our sales people can’t purchase something without technical oversight and approval,” he said. “That’s how we control it.”
A report by the Aerospace Industries Association said the supply chain suffers if counterfeit parts, whether they are electronic, mechanical or other, make their way into stock and on to aircraft. It cites security and safety risks, costs to mitigate risk and replace failed parts, and reputational damage, among others.
Recently the US Department of Transportation’s inspector general criticised the FAA for “ineffective” oversight of industry actions to remove SUPs from the aviation system.
This prompted US Congressman Peter DeFazio, from Oregon, to point a finger of blame at MROs outside the US. “A lot of our airlines have outsourced their heavy maintenance overseas, where one criminal could put in a part that’s going to cause a critical failure in that aircraft.”
These fears were compounded by a whistleblower, who claimed some parts manufactured in China were made with inferior materials and processes, and then shipped with fabricated documentation to conceal the violation.
With demand for spares on some popular engines predicted to outstrip supply from next year, the pressure to cut corners can be a concern.
Analysing forecasts for CFM56-7B and -5Bs and V2500s, aviation consultancy IBA says the spares problem is exacerbated for MROs and operators because there are so many of these engines flying.
Spares are currently in very limited supply and unless more are generated by engine retirements and aircraft teardowns, or airline-held spare stock absorbs some of the demand, IBA expects engine inductions and longer turn-around times (TATs) will create an MRO logjam.
However, an IBA spokesman pointed out that the aviation part supply market is highly regulated and controlled. “We are confident that the safeguards in place throughout the supply chain are sufficiently robust to cater for all situations and do not see that parts shortages would result in a risk that standards would be compromised.”
Elsewhere, the industry has taken steps to reinforce these controls. In 2015, a cooperative industry effort resulted in the launch of the counterfeit avoidance accreditation program (CAAP). Run by the not-for-profit Performance Review Institute (PRI), it aims to mitigate both the risk of introducing counterfeit parts into the supply chain and the cost of compliance.
The Coalition Against Counterfeiting and Piracy (CACP), set up by the US Chamber of Commerce, says the long life cycles of aerospace and defence, plus diminishing sources of supply and material shortages, make them attractive targets for counterfeiting. CACP produces a manual on the subject for industry.
Certification to the AS9100 standard requires organisations to take steps against counterfeit products. These broadly include staff awareness training; selecting and buying only from trusted sources, who guarantee traceability of parts; robust inspection, testing and verification to prevent counterfeits from entering stock; and monitoring the obsolescence of parts to make design decisions appropriate to the service life of the product.
Stay up to date
Subscribe to the free Times Aerospace newsletter and receive the latest content every week. We'll never share your email address.