Gloss leaders
Geoff Thomas gets under the skin of aircraft painting to understand coatings.
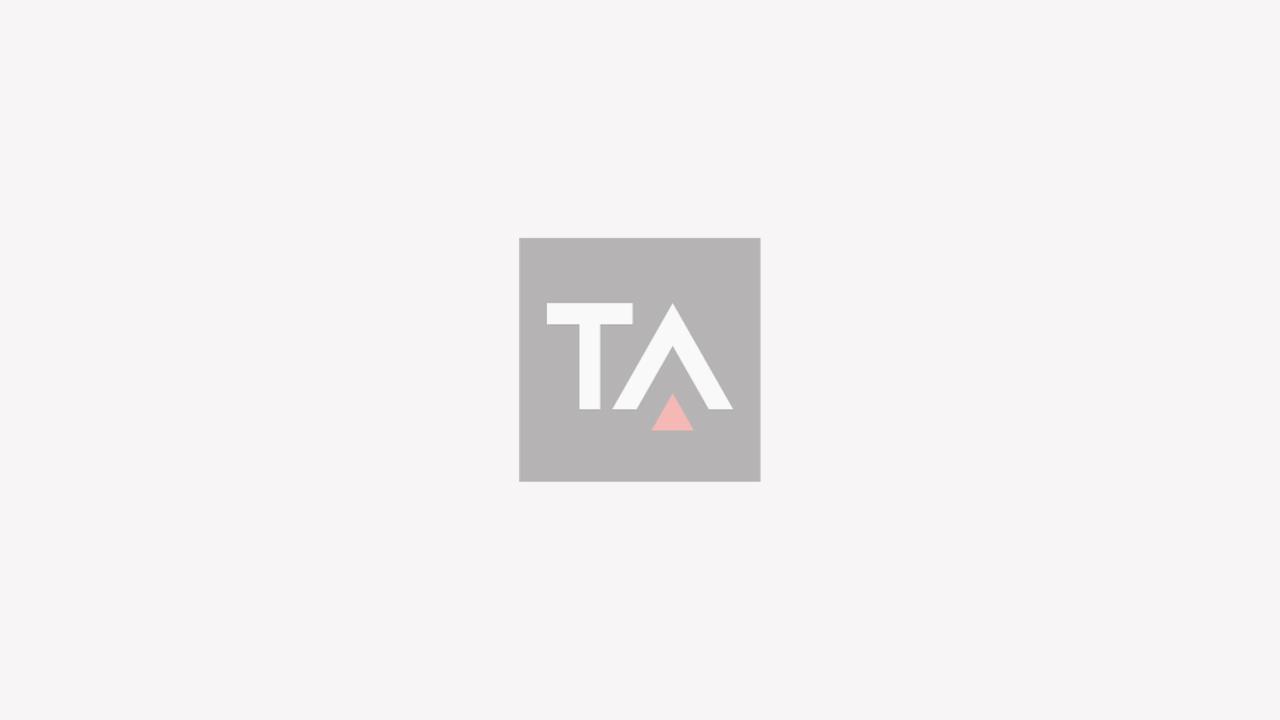
Next time you fly in an airliner from one of the major Middle East-based carriers, there’s an 80 per cent chance that the glossy exterior paintwork will have been applied using products from Dutch-based company AkzoNobel Aerospace Coatings.
Although the company doesn’t employ the people who actually apply the paints (that’s all done by each airline’s in-house or sub-contracted paint teams) it does take great pains to train operators, helping to ensure that each airframe looks its best and also that the potential weight-saving over previous painting techniques (only if the paint is correctly applied) is realised.
AkzoNobel Aerospace Coatings’ sales manager for the Middle East is Dutchman René Bremer, who has worked in the region for more than a decade.
“Because so many of the airlines in the region are among the best in the world, they require their aircraft to have a particularly ‘distinguished image’,” he said. “To this end, they want them to look shinier and more glossy than the international competition and our fast-drying ‘base coat/clear coat’ method, using newly-developed polyurethane paints/lacquer, enables this to happen while also saving them money in several important ways over the lifetime of the airframe.
“Our method results in an ultra-shiny surface that improves the appearance and provides less dirt pick up. Extended cleaning cycles also require less water and easily keep the aircraft shiny thanks to the clear coat system. This also dovetails in with the sustainability programmes of all regional airlines.
“And, while a standard ‘paint job’ lasts for around four to six years in the harsh North African and Middle Eastern climate and environment, our new product gives up to eight years’ service before it needs replacing, resulting in yet more cost-savings.”
Dust, salt and sand being blown around during take-off and landing – especially when combined with intense sunlight and vast temperature ranges – results in a highly abrasive and damaging cocktail of challenges for the paint on aircraft, explained Bremer.
“Our latest technology provides an even better performance in these harsh conditions. Despite weighing less, the new method actually gives better protection, coverage and colour depth than previous paints and it takes less time to dry (two hours instead of overnight between the application of different colours) which again means less down-time and further potential cost savings.”
According to Bremer, the key to the huge success in the region of the AkzoNobel product is in the comprehensive on-site training process and local technical presence.
“It’s an intense programme,” he explained, “and we insist on using the airline’s own spraying equipment so that we can demonstrate just how the new products will look in reality, rather than on the page of a sales brochure.”
Because the drying time is so much less than for conventional, classic high solid paints, it’s also possible to be far more creative with the designs. And it’s for this reason that so many airlines in the region are now experimenting with more ornate and eye-catching liveries like the one that featured on some of Etihad’s fleet to promote Abu Dhabi’s links with the exciting world of Formula 1 motor sport.
When AkzoNobel introduced the clear coat programme in 2006, it was delighted that the uptake by the airlines was so enthusiastic.
“It’s a win-win situation,” concluded Bremer “We provide our high-tech coatings and services that combine to allow our customers to fly beautiful, glossy aircraft. The new technology improves the appearance and reduces the coating maintenance costs to a minimum.”
Stay up to date
Subscribe to the free Times Aerospace newsletter and receive the latest content every week. We'll never share your email address.