Keeping up appearances
Emirates' unique 'Aircraft Appearance Centre' is gearing up for full operation. Following a soft opening in August 2010, six aircraft have been completed and a full back-to-back schedule is due to start in August this year.
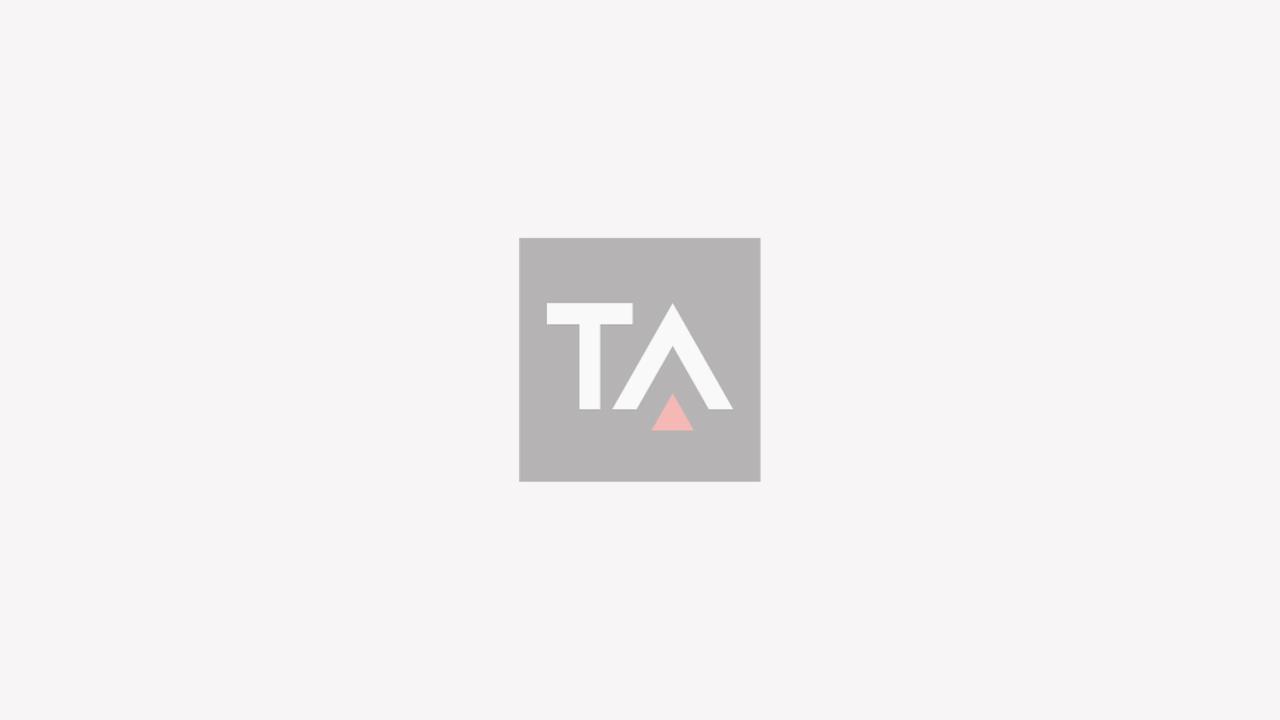
Built at a cost of around Dhs150,000 and equipped to the highest technical specs, the facility will employ 64 specialist staff drawn from around the world.
From August this team expects to process two aircraft per month, opening just as many of the Emirates fleet are due to be repainted.
The airline estimates that use of the onsite facility will cut repainting costs by up to 55 per cent compared with outsourcing the work to European suppliers.
The 12,000sqm hangar is based on the design of the Airbus A380 paint hangar in Hamburg. The difference is that the Emirates facility will handle a range of aircraft from a Boeing 737 to the vast A380.
The explosion-proof hangar is equipped with six teleplatforms, costing around $750,000 each, scissor platforms and under-aircraft access stands for safe and efficient access to all areas.
The main challenges for the management team are environmental. The building has to maintain positive pressure to keep the dust out and be sealed to preserve the carefully regulated temperature and humidity, despite sometimes extreme outside conditions. Martin Taylor, shift manager at the centre, explained: “There are strict parameters when using aviation paint. The humidity has to be within one or two per cent to avoid defects in the finish, such as orange peel, blooming and blisters. Emirates has incredibly high standards for the work. While the original equipment manufacturer (OEM) sets the orange peel standard at eight, Emirates ups that figure to 12. If it falls below, we have to start again.”
Quality is paramount here, with thousands of dollars having been spent on testing equipment. Taylor said: “Quality is second only to safety and is constantly checked. We have a wave-scan machine to test the orange peel effect and a gloss level tester as well as the dry film thickness gauge to ensure the paint is no more than 400 microns thick. There is no compromise.”
The Appearance Centre has fully-automated environmentally-controlled systems. The air-conditioning system within the hangar is completely computerised and designed to avoid dead areas, where paint may be slower to dry.
Bob Lunn, vice president engineering facilities, explained: “The system controls the lighting and airflow during each phase of the sealing, stripping and painting according to aircraft type and paint type. Specially placed vents on the walls and ceiling blow air over the fuselage and wings as if the aircraft were flying. This avoids dead spots, such as on the underside of the wings, which can remain wet longer and affect the finish.”
The new facility is also as green as possible, given the work performed. Lunn said: “We use non-toxic environmentally friendly paint strippers, but what we are removing from the aircraft contains hazardous materials – chromates in the paint, aircraft fuel, hydraulic fluids, grease. Everything is washed down into tanks below the hangar, where the solid waste is separated from the water. The water is reused and a specialist company takes the solid waste for disposal.
“We also have a solvent recovery machine in our cleaning area. When the brushes and spray guns are washed, the solvent is separated from the solid waste and reused, while the gel-like waste is disposed of safely.”
All the air blown over the aircraft is sucked into gratings, where it is filtered to remove dust and paint particles.
Each wide-bodied aircraft will take between 10 days to two weeks to complete, depending on type. Before it can be stripped and painted, the aircraft has to have all fuel removed and then it is completely sealed to ensure no paint goes into the cockpit or cabin.
While the Airbuses are only stripped to primer level, the Boeings are taken back to bare metal for a mandatory check of the entire airframe.
“We are checking for scribe marks,” said Lunn, “which can cause flaws and cracking. These marks are from engineers marking the aluminium for any reason when working on the aircraft, or they can be from the use of a knife or screwdriver to remove a decal. Once the top aluminium is scored it is an opening for corrosion.”
Once inspected and approved, each aircraft receives three coats of white paint, the solid colours and then a clear coat lacquer.
Lunn said: “The harsh climate of the Middle East means that colours fade and white paint yellows more quickly than in Europe. The clear coat extends the life of the paint. Without it we can expect to repaint every four to five years. Clear coat protection extends that to six to seven years.”
While some paint is supplied by industry giant AkzoNobel, Taylor has been delighted to find a local supplier in Dubai.
“We have begun to use PPG, which is based in Jebel Ali in Dubai. It offers the same high quality, but whereas an order from the UK has a 45 day lead time, these are available straight away. We would normally order around four sets from a European supplier; now we can order one at a time. This cuts down the amount of capital tied up in inventory, eliminates storage issues and shelf life considerations and, of course, the cost of shipment.”
The PPG paint is also designed to suit the local climate and can be used in 20-30 per cent higher humidity conditions. “This again is a cost saving as we do not have to run the very expensive electric heaters we use to reduce humidity,” he added.
In addition to the main hangar, the Emirates Engineering Paint Shop handles around 3,000 items per month in three custom-built paint bays. The items sprayed range from internal components, such as seat shells, meal trays, toilet seats and overhead lockers to wheels, flaps and ailerons.
Taylor said: “Much of this work was done in situ previously, which required the painters
to tent the part in the hangar. This was much more challenging to maintain the temperature and quality and time consuming.”
The three booths allow swift work, faster drying and the use specialist paints, such as the pearlised paint used on seats in the Business Class cabins.
The facility is unique in the region and Emirates has previously discussed offering MRO support to third-parties, so will we see other airlines’ aircraft rolling out of the hangar? Lunn considers it unlikely, but does not rule it out completely.
“In the short term we expect to be fully utilised with the Emirates fleet. However, should an aircraft be pulled from the paint line for any reason, a slot may become available and we have to be aware of the commercial interests.”
Lunn concluded: “The external appearance of an Emirates aircraft is an essential part of the image of the airline. There is now additional pressure on us to maintain that pristine appearance as most of the new terminals and first class lounges offer panoramic views of the runway. A tatty looking plane does not inspire confidence in the airline and we now have the facility to ensure that Emirates’ aircraft never fall short of the high standards that are set.”
Stay up to date
Subscribe to the free Times Aerospace newsletter and receive the latest content every week. We'll never share your email address.