Emissions: The Big Issue
Driven by ever-increasing oil prices and growing environmental concerns, the world of commercial aerospace is moving into a new and exciting era of research and development. Geoff Thomas reports.
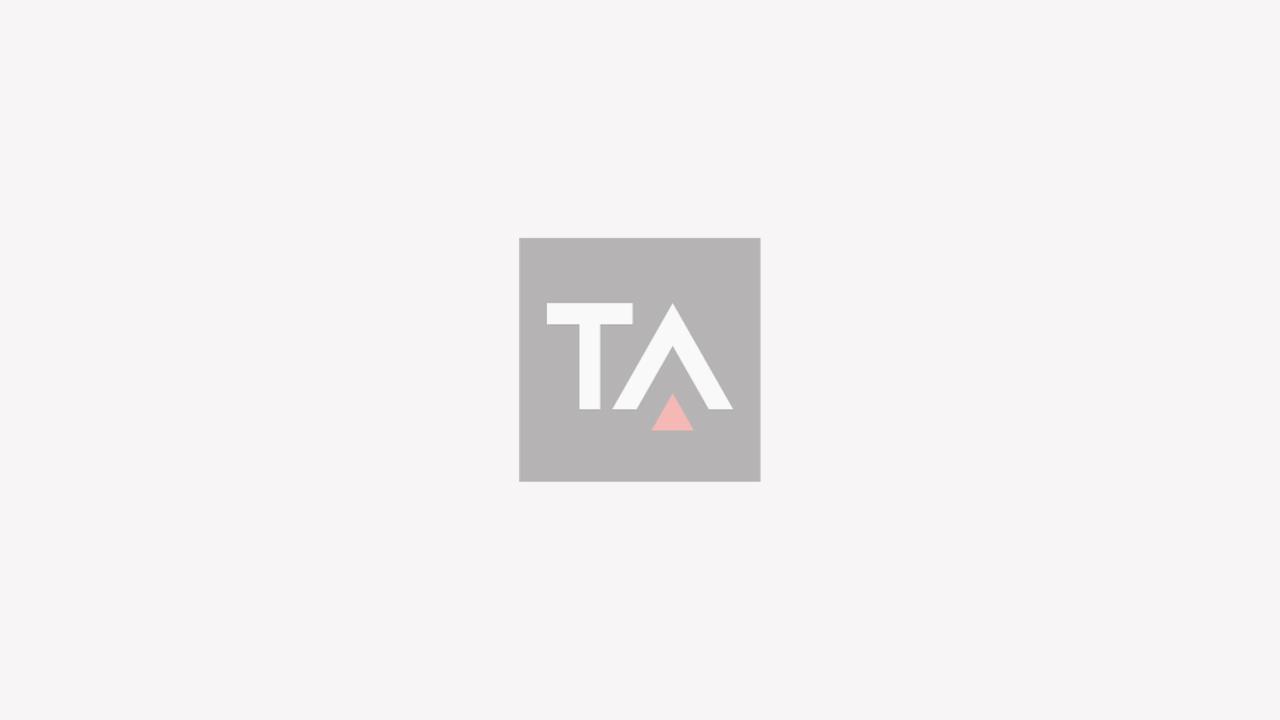
While an airliner’s engines produce the thrust that enables flight to happen, it’s those self-same noisy and relatively smoky fuel-guzzlers that create many of the negatives in the industry. Without them there would be no commercial flying – but with them there are distinct perceived disadvantages.
Although many believe the vigorous response of the naysayers to be disproportionately negative (for political and publicity reasons), both noise and emissions have been under the environmental spotlight for many years. Consequently, addressing these issues is at the centre of thinking by the engineers, who are working on creating game-changing technologies and entire powerplants.
It’s likely to be at least a decade before anything that provides the level of fuel saving that airlines crave – or the quieter and less polluting engines demanded by the environmentalists – actually takes to the skies. However, improvements are introduced regularly with each new development and upgrade.
Ever since the turbojet engine was first developed in the 1930s and 1940s, progress has been extraordinarily fast. And since the development of the high-bypass ratio turbofan engine around half a century ago, improvements in fuel burn have worked out on average at around 1% per year.
Aviation currently accounts for only around 2% of man-made CO2 emissions but it’s true to say that the sector’s growth – along with the adoption of low-carbon technology in other sectors – means that commercial aviation’s production of this so-called ‘greenhouse gas’ will increase in both absolute and relative terms over the coming decades.
And despite the fact that scientists confess to not fully understanding the impact of high-temperature generated oxides of nitrogen (NOx) on the atmosphere (where, incidentally, one of the larger sources is lightning flashes, each one resulting in around 7kg of NOx being produced) it’s generally accepted that the gas is not a good thing. However, trading this off in engineering terms against reducing fuel-burn is a complex issue, as one of the best ways of decreasing the use of kerosene is to increase the temperature of the engine’s core and it’s this, in turn, that increases the production of NOx, which is a product of high temperatures.
So while NOx emissions undoubtedly contribute to air quality concerns near airports, and noise is an issue for people who live close to major airports, these interlinked environmental concerns present a highly complex design problem. The means of reducing one impact can lead to increasing challenges in other areas.
The aviation industry has a strong track record of reducing these impacts, investing consistently in product technology over the past six decades. Aircraft today are 75% quieter and use 70% less fuel (when calculated on a passenger-per-kilometre basis) than the earliest jet airliners like the de Havilland Comet and the Boeing 707.
British engine OEM Rolls-Royce claims that its Trent 1000 engine, that flew for the first time on the Boeing 787 Dreamliner in December 2009 and is now in service around the world, is 25% more fuel efficient than its RB211 jet engine that powered the Lockheed Tristar. It was that engine, coincidentally, that led directly to development of today’s family of Trent engines and bankrupted Rolls-Royce in its earlier manifestation.
The Advisory Council for Aeronautics Research in Europe (ACARE) has published targets that are running in parallel to similar ones in the USA, and are set to be achieved by 2020.
From a 2000 baseline, Europe is aiming to: Reduce CO2 emissions per passenger kilometre by 50%; reduce NOx emissions by 80% and reduce perceived aircraft noise by a half.
The ACARE NOx target includes total NOx emissions produced over a flight. Improvements in engine technology are expected to deliver three-quarters of the 80% with the balance coming from the overall reduction in fuel burn as a result of improved efficiencies in engine, airframe and operations.
Meeting the CO2 target requires improvements of 15-20% for engines, 20-25% for aircraft and 5-10% from air traffic management.
Since the first Trent engine entered service 15 years ago, Rolls-Royce has introduced five additional members to the family. The Trent 1000 is 12% more fuel efficient than the Trent 800 and the latest variant, the Trent XWB for the Airbus A350 airliner, will give a 16% improvement in fuel efficiency when compared to the first Trent in service.
Like all the world’s engine OEMs, Rolls-Royce aims continually to improve on engine efficiency and it has announced a decision to target two wholly new families of two-shaft and three-shaft turbofan engines in the 2020s. In the longer term, it continues to see ‘open rotor’ technology as a potential step change in performance and in conjunction with new partner in this arena, Pratt & Whitney, is currently targeting entry into service for towards the end of next decade for this technology.
However, the integration of open rotor into the airframe will present new challenges for the industry. Rolls-Royce’s engine product strategy for 2010-2025 means that it will have engines entering service that, on average, will reduce the fuel burn of aircraft replaced in that 15-year period by at least 15%.
A conventional turbofan aircraft engine generates most of its thrust from a large front-mounted fan, enclosed in a fan-case and nacelle. Engines can be made between 10% and 15% more fuel-efficient (than a future advanced turbofan) by dispensing with the fan-case and designing the fan to operate as an open rotor. The open rotor concept, therefore, uses large unducted fan blades, creating a powerplant with much of the fuel-efficiency of a turbo-prop engine.
The Derby-based company began wind tunnel tests for its open rotor system in 2008 and 2009 in the Netherlands and the UK and these surprisingly showed that, as well as being more efficient, the engines were quieter than existing types and would meet future noise legislation.
But it’s not only in the UK and Europe that research into the next generation of commercial engines is bearing fruit. Both GE and Pratt & Whitney are developing ground-breaking designs and concepts – in P&W’s case, the geared turbofan engine, now known as the PW1000G, that is slated to power Bombardier’s CSeries, the Mitsubishi Regional Jet (MRJ) and the Irkut MS-21 (all newly-developed single-aisle airliners) and is also being offered as an option on the Airbus A320neo.
In the case of the PW1000G, the engine has a gear system to drive the front-mounted fan at an ideal speed more suited to improved economy and lower noise.
But it’s not only within the realms of civil aerospace that improvements to commercial engines are created. In the case of the world’s most popular engine (the CFM56 family that powers Boeing 737s and the Airbus A320 family of airliners) it’s the subtle combination of the US Navy and Air Force that stand to save more than $2-billion after jointly developing an engine modification that will keep critically important aircraft flying for years – technology that’s bound to find its way into older airliners that are still flying in many parts of the world.
The two services and industry worked together to develop and field a modification to CFM International’s CFM56-2 (F108) engine, allowing them to restore exhaust gas temperature (EGT) margins, increase fuel economy and extend time between overhauls from 10 to 15 years.
The CFM56 engines are used on the Navy’s E-6B Mercury command and control aircraft and the Air Force’s C-135 series tankers and reconnaissance aircraft.
CFM International (CFM), the engine’s maker, received FAA certification of the modifications a couple of months ago.
Both the US Navy and the Air Force were struggling to reclaim lost engine efficiency after first overhaul with only half of the engine life being regained.
About four years ago, the Navy CFM56 engine team, having exhausted all known means to reclaim lost engine performance, asked CFM to make design improvements. That effort paid off and resulted in submitting a proposal for commercially proven design improvements used in newer models of the CFM56 engine family.
Realising that incorporating these improvements were too costly for the Navy to implement on its own, it approached the USAF and the subsequent coordination resulted in a plan advantageous to both services with costs and ground testing being shared.
Over the next few months, the updated engine would be tested, overhauled and tested again four times. This extensive barrage of ground testing helped reduce the amount of flight test time required and provided CFM engineers with a controlled environment to capture FAA certification data. When the ground tests were complete, the engine was rebuilt and certified ready for flight tests by Navy and CFM engineering.
This joint service engine upgrade programme will provide both the Navy and Air Force with huge cost savings over its life and now the team is involved in coordinating acquisition and logistics to incorporate design improvements into the engines at the Oklahoma City Air Logistics Center during depot-level overhauls for Navy and Air Force aircraft next year.
Earlier this year, CFM International, along with other key aviation leaders, co-signed a declaration to broaden the industry’s commitment to action on climate change with a goal to advance and strengthen the interdependent pillars of sustainable development.
Like the other major engine OEMs over the past 35 years, CFM has introduced revolutionary technologies to improve engine performance. With its CFM56 engine family, the company has established a track record of continuous innovation and improvement that has helped set new performance standards.
This tradition seems set to continue with the introduction of the advanced LEAP engine family. This all-new engine will help establish even higher standards for aircraft engine noise and emissions without any compromise in economics, giving operators better fuel efficiency and economical operating costs.
CFM claims that for each old aircraft replaced, its LEAP engine can eliminate as much as 11,000tonnes of CO2 emissions per year, depending on the age of the engines being replaced.
The major engine builders’ on-going investment in engine technologies will help support the industry’s commitment to meet the 2020 goal of carbon-neutral growth, while at the same time developing longer-term technologies, including engine architectures like the open rotor, which could help address the ambitious target of a 50% reduction in carbon emissions by 2050.
The joint declaration that brought together ‘thought leaders’ from across the industry, will support a global collaborative structure that can accelerate collective ability to meet the environmental challenges of the future, said Jean-Paul Ebanga, president and CEO of CFM International. He continued: “We know that this kind of global partnership is critical and we are happy to lend our full support and expertise to the Air Transport Action Group (ATAG) initiatives.”
Stay up to date
Subscribe to the free Times Aerospace newsletter and receive the latest content every week. We'll never share your email address.